- The liquid-gas separator should be tested after installation. Pour clean water or drilling fluid into the separator until there is liquid flowing out of the outlet pipe.
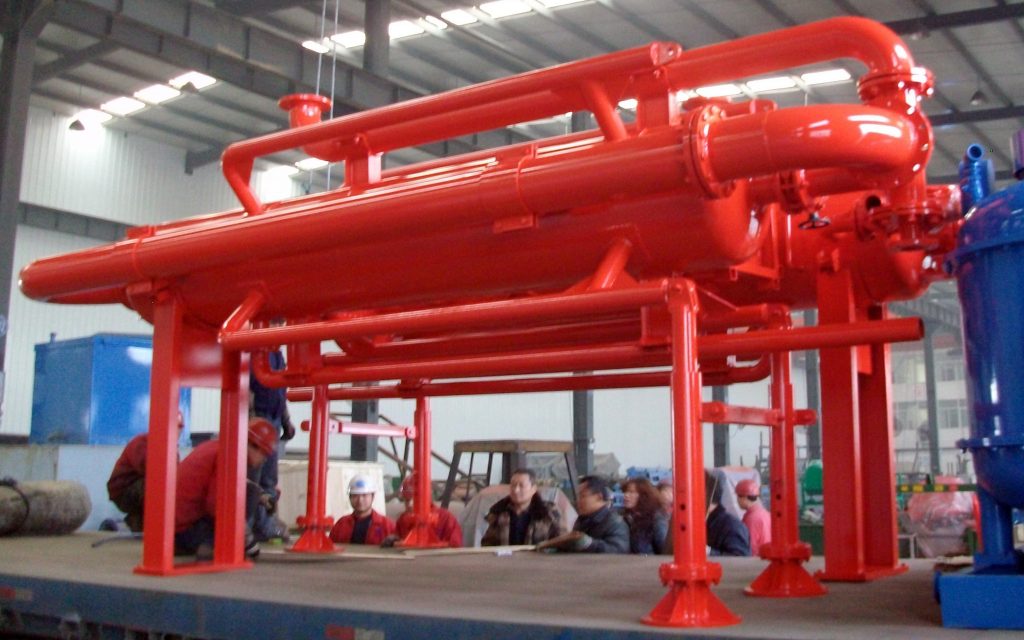
2, before use, the maximum allowable working pressure should be calculated according to the measured effective height of U-shaped tube and drilling fluid density (maximum allowable working pressure Pmax= effective height of U-shaped tube H× drilling fluid density ρ).
3, before entering the oil and gas reservoir, the cadre on duty or the driller should check the liquid gas separator:
(1) The stop valve under the pressure gauge is normally open.
(2) The safety valve is in normal working condition (the safety valve handle is perpendicular to the ground). Before installation, before opening the oil and gas reservoir, and every 30 days during operation in the oil and gas reservoir, the safety valve is activated by turning the handle in the counterclockwise direction.
(3) The pressure measuring flange globe valve is normally open.
(4) The stop valve is closed after the exhaust pipeline blowdown.
(5) The ignition device is complete.
4, the external fitter for each shift of liquid gas separator and its accessories tour inspection, focusing on the tank, pipeline, safety valve, pressure gauge, fasteners, such as appearance inspection, found problems timely rectification.
- After the liquid-gas separator is put into use, if the separated gas contains hydrogen sulfide, carbon monoxide or flammable gas, warning measures should be taken, and the ignition operation instructions should be issued by the cadre or technician on duty, and the ignition process should be supervised.
6, the ignition operation is implemented by the external fitter, and the ignition process should follow the procedure of first ignition and then operation. - During the use of the liquid-gas separator, special personnel should be arranged to observe the return of drilling fluid from the liquid outlet, the vibration of the liquid inlet pipeline and the pressure of the exhaust pipeline, monitor the flame height, and ignition should be carried out again when the flame is extinguished. When one of the following abnormal phenomena is found, it should be stopped immediately and reported in time.
(1) There is gas discharge at the outlet of the drain pipe or liquid discharge at the outlet of the exhaust pipe.
(2) The exhaust pipe pressure gauge reading is greater than the maximum allowable working pressure calculated.
(3) The main pressure elements of the liquid-gas separator appear cracks, bulging, deformation, leakage and other defects.
(4) Safety accessories such as safety valves and pressure gauges fail.
(5) The seal or fixed damage of liquid intake pipeline, liquid discharge pipeline, exhaust pipeline, fasteners, etc.
(6) Severe vibration of liquid-gas separator and pipeline threatens safe operation. - When the wellbore is full of gas, it is prohibited to use a liquid-gas separator.
- It is strictly prohibited to perform electric welding operations on the liquid gas separator tank, liquid intake pipeline and exhaust pipe line.
maintenance
After the use of the liquid-gas separator, the following maintenance should be done:
one Clean the inside of the liquid-gas separator with clean water.
- Open all blowdown valves, and timely discharge the residual drilling fluid or water in the separator tank, liquid discharge and exhaust pipeline.
- Check, tighten and maintain connection bolts and platen bolts.
- During winter construction, heat preservation and anti-freezing measures should be taken for liquid inlet pipeline and blowdown valve of liquid-gas separator.
- If the site use time reaches one year, the well control equipment maintenance unit shall conduct inspection and maintenance, and issue inspection and maintenance report.
6 Every three years should be in accordance with the “Special equipment safety Technical specifications: Fixed pressure vessel safety technical supervision regulations” (TSG21-2016) requirements, by the inspection qualification of the organization to carry out an internal and external inspection of the liquid gas separator. If the corrosion rate of the main material of the separator is greater than 0.3 mm/year, the period of internal and external inspection should be appropriately shortened. - The safety valve and pressure gauge should be checked once a year.